Why are aluminum products not easy to weld?
Oct 30, 2023
While welding aluminum can be difficult, it’s a skill that can be developed with the right knowledge and practice. Keep reading to learn all about how to weld aluminum—from the different types of welding you can use to general tips for success.
1. Aluminum is highly prone to oxidation in the air and during welding. The resulting aluminum oxide (Al2O3) has a high melting point, is very stable, and difficult to remove. It hinders the melting and fusion of the base material, and its high density makes it challenging to float to the surface. This can lead to the formation of inclusions, incomplete fusion, and inadequate penetration. Aluminum materials tend to have surface oxide films and adsorb a significant amount of moisture, which can lead to the formation of weld pores.
Prior to welding, strict surface cleaning through chemical or mechanical methods is necessary to eliminate the surface oxide film. During welding, enhanced protection is required to prevent oxidation. When using tungsten inert gas (TIG) welding, alternating current (AC) power sources are chosen to facilitate "cathode cleaning" for oxide removal. When gas welding, flux is employed to remove oxide films. In the welding of thick plates, increasing welding heat input can be beneficial.
For example, using helium as the shielding gas or helium-argon mixtures, or employing large-diameter consumable electrode gas metal arc welding (GMAW), "cathode cleaning" may not be necessary when using direct current (DC) positive polarity.
Melting point | 933.47 K (660.32 °C, 1220.58 °F) |
Boiling point | 2743 K (2470 °C, 4478 °F) |
Density(near r.t.) | 2.70 g/cm3 |
Hear of fusion | 10.71 Kj/mol |
Thermal expansion | 23.1 µm/(m⋅K) (at 25 °C) |
Thermal conductivity | 237 W/(m⋅K) |
Electrical resistivity | 26.5 nΩ⋅m (at 20 °C) |
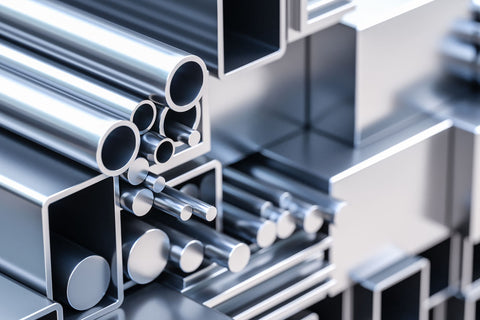
2. The thermal conductivity and specific heat capacity of aluminum and its alloys are both approximately more than twice that of carbon steel and low-alloy steel. In contrast, the thermal conductivity of aluminum is several times higher than that of austenitic stainless steel. During the welding process, a significant amount of heat can be rapidly conducted into the base metal.
Therefore, when welding aluminum and its alloys, energy is not only consumed in melting the welding material but also dissipates in the surrounding metal areas. This wasteful energy consumption is more pronounced in aluminum welding compared to steel welding. To achieve high-quality welding joints, it is advisable to use concentrated energy sources with high power whenever possible. In some cases, preheating and other process measures may also be employed.
3. The linear coefficient of thermal expansion for aluminum and its alloys is approximately twice that of carbon steel and low-alloy steel. Aluminum experiences a significant volume shrinkage during solidification, leading to greater distortion and stress in welded components. Therefore, measures to prevent welding deformation should be implemented. When aluminum weld pools solidify, they are prone to developing shrinkage cavities, porosity, hot cracking, and higher internal stresses.
In production, adjustments to the composition of the welding wire and welding processes can be made to mitigate the formation of hot cracks. When corrosion resistance allows, aluminum-silicon alloy welding wires can be used for welding aluminum alloys other than aluminum-magnesium alloys. The tendency for hot cracking is more pronounced when silicon content is around 0.5%. As silicon content increases, the alloy's crystallization temperature range becomes narrower, fluidity significantly improves, shrinkage rates decrease, and the susceptibility to hot cracking decreases accordingly.
4. Aluminum has a strong ability to reflect light and heat; when solid and liquid transition, there is no obvious color change, making it difficult to judge during welding operations. The strength of high-temperature aluminum is very low, it is difficult to support the molten pool, and it is easy to weld through.
5. Aluminum and aluminum alloys can dissolve a large amount of hydrogen in the liquid state, but hardly dissolve hydrogen in the solid state. During the solidification and rapid cooling process of the welding pool, hydrogen has no time to escape and hydrogen holes are easily formed. The moisture in the arc column atmosphere, the moisture adsorbed by the oxide film on the surface of the welding material and the base metal are all important sources of hydrogen in the weld. Therefore, the source of hydrogen must be strictly controlled to prevent the formation of pores.
6. Alloy elements are easy to evaporate and burn, which reduces the performance of the weld.
7. If the base metal is deformation-strengthened or solid-solution age-strengthened, the welding heat will reduce the strength of the heat-affected zone.
8. Aluminum has a face-centered cubic lattice and has no allotropes. There is no phase change during heating and cooling. The weld grains tend to become coarse and the grains cannot be refined through phase changes. Welding methods Almost all welding methods can be used to weld aluminum and aluminum alloys, but aluminum and aluminum alloys have different adaptability to various welding methods, and each welding method has its own application.
Gas welding and electrode arc welding methods are simple in equipment and easy to operate. Gas welding can be used for repair welding of aluminum sheets and castings that do not require high welding quality. Electrode arc welding can be used for repair welding of aluminum alloy castings. The inert gas shielded welding (TIG or MIG) method is the most widely used welding method for aluminum and aluminum alloys.
Aluminum and aluminum alloy sheets can be welded by tungsten electrode alternating current argon arc welding or tungsten electrode pulse argon arc welding. Aluminum and aluminum alloy thick plates can be processed by tungsten helium arc welding, argon-helium mixed tungsten arc welding, gas metal arc welding, and pulse metal arc welding. Gas metal arc welding and pulse gas metal arc welding are increasingly used (argon or argon/helium mixture).
Now, let's explore how to tackle these aluminum welding challenges. To assist you in achieving high-quality aluminum welds, we strongly recommend using our aluminum welding machine: MIG-250D. This welding machine boasts a range of powerful features that make aluminum welding easier and more efficient. Let's delve into its advantages and how to leverage it for outstanding welding results.
Types of Aluminum Welding
If you’re wondering how to weld aluminum, it’s important to know that there are several welding processes that can be used:
GTAW/TIG
Gas tungsten arc welding (GTAW), also known as tungsten inert gas (TIG) welding, is one of the most popular welding processes chosen for aluminum. This welding technique is often used by automotive enthusiasts and welders for professional racing teams.
GTAW requires a constant current equipment with AC (alternating current) capabilities using 100 percent argon as a shielding gas. It does not require mechanical wire feeding, which has the potential to create feedability issues.
Rather, the welder will feed the filler material into a puddle. This process is also very clean, as the alternating current cleans the oxidized layer off the aluminum as it welds. It also prevents aluminum from being contaminated throughout the process.
Tips for TIG welding:
- Pick the right tungsten electrode or rod—the best choice for aluminum is typically a pure tungsten rod
- Take the time to prepare your aluminum by cleaning and preheating it
- Ensure there is not too much argon flow at the torch, which can cause an irregular arc
- To prevent warping, use a heat sink
- When welding, keep the proper aluminum filler electrode or rod free of contaminants and melt it with the base material to create a constant welding puddle
GMAW/MIG
Gas metal arc welding (GMAW), commonly referred to as metal inert gas (MIG) welding, is another common method used for aluminum welding.
This type of welding typically has faster travel speeds and higher deposition rates than TIG welding, affecting the weld quality. However, it does utilize a mechanical wire feeding system, which means the welder may have to use a spool gun or push-pull gun to make wire feeding possible.
Additionally, in order to combat the risk of aluminum becoming porous, the base material and filler rod must be clean, free of moisture and have excellent shielding gas coverage, typically pure argon content. Check out Lincoln Electric’s guide to aluminum GMAW welding to learn even more about this method.
Tips for MIG welding:
- Prepare your push-pull wire feed
- Clean your aluminum, remove any oxide and file the edges that will be joined
- Avoid pulling while welding—instead, push at a 10 degree to 15 degree angle
- Use multiple pass straight beads to improve the overall appearance of the weld and help to avoid defects
- Use a heat sink, which will absorb extra heat and allow you to weld slower
Things to Avoid When Welding Aluminum
Now that we’ve covered different methods that can be used to weld aluminum, let’s talk about some common mistakes to avoid.
- Taking a “one-size-fits-all” approach: When it comes to welding aluminum, the welder must take an entirely different approach than they would with a material like steel. It’s critical for the welder to not base their technique on experience they have with other metals or materials, as aluminum is very unique and can present dangers when not handled correctly.
- Not wearing the proper PPE: Speaking of dangers, welding aluminum or any kind of material is inherently dangerous. It’s important for welders to always wear the correct personal protective equipment (PPE) and educate themselves on safety procedures and best practices. This is key to a long, successful career in the industry.
- Failing to prepare: Preparation is key—both for the welder and the material being welded. Always be sure to properly clean your aluminum and store it correctly before beginning your weld. Additionally, make sure to prepare yourself by studying the art of aluminum welding and educating yourself on the craft. Never jump into anything until you are adequately prepared.
- Ignoring minor details: The most successful welders will tell you that detail is everything. In this industry, the smallest misstep can lead to a complicated error—especially with aluminum welding. Always pay attention to every detail and double check your work, as this will benefit your customers and your career in the long-run.
- Not being patient: Learning to weld aluminum takes time. Keep practicing and stick with it—your hard work and persistence will pay off in the end!
What is the Best Method to use for Welding Aluminium?
The best method to weld aluminium and its alloys is dependent on the joining application of interest. The following points should be included for consideration before deciding on a welding process:
- Cost (welding equipment, consumables, waste disposal, operator costs, etc)
- Desired weld performance
- Geometric constraints
- Supplier availability
- Repeatability
- Distortion tolerance
- Speed of production
- Health and Safety
MODELS/Parameters | MIG-250D |
Rated Input Voltage(V) | 220±15% 110±15% |
Input Frequency(Hz) | 50/60Hz |
Rated Power(KV.A) | MMA:7.2@220V |
MMA:4.9@110V | |
MIG:6.3@220V | |
MIG:4.2@110V | |
Rated Input Voltage(V) | MMA:33@220V |
MMA:45@110V | |
MIG:29@220V | |
MIG:39@110V | |
No-load Voltage(V) | 60 |
Rated Output Current(A) | MMA:20-200 |
MIG:40-200 | |
Duty Cycle(%)@25C | 40% |
Power Factor | 0.7 |
Efficiency(%) | 85 |
Insulation Class | F |
Protection Class | IP21S |
Welder Weight(ibs) | 22 |
Welder Size(inches) | 18.1*9*16.5 |